Hydraulic Oil Seal Innovations Improving Equipment Longevity
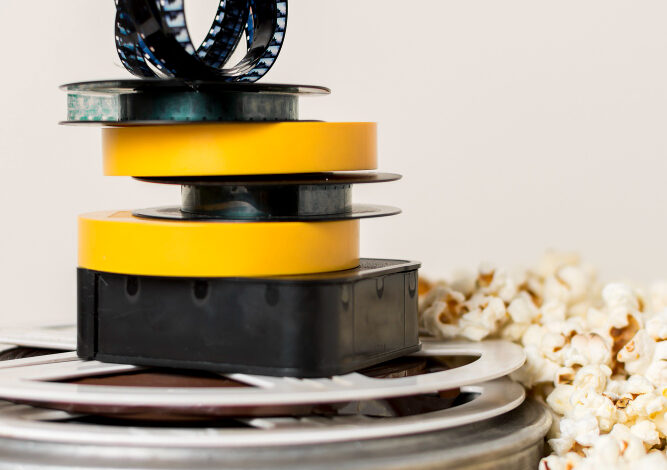
In the demanding world of industrial machinery and fluid-powered systems, even the smallest components play a critical role in performance and reliability. Among these, the hydraulic oil seal stands as a silent yet vital guardian, preventing leaks, maintaining pressure, and ensuring equipment durability over time. As industries push the boundaries of performance, the evolution of hydraulic oil seal technology has become essential to achieving greater operational efficiency and extending equipment lifespan.
Understanding the Function of a Hydraulic Oil Seal
At its core, a hydraulic oil seal—also referred to as a fluid seal or shaft seal—is designed to contain hydraulic fluid within systems while preventing contaminants like dust, dirt, and moisture from entering. These seals operate under extreme pressure and temperature conditions, often in abrasive or corrosive environments.
By effectively maintaining the integrity of hydraulic cylinders, pumps, and other components, these seals play a key role in preserving the performance of critical systems. However, failures in sealing mechanisms can result in costly leaks, equipment damage, and even safety hazards. Therefore, this underscores the importance of investing in precision-engineered sealing solutions.
The Evolution of Seal Technology
Over the past decade, hydraulic oil seal technology has undergone significant innovation, driven by increasing performance demands in sectors such as manufacturing, logistics, construction, and energy. Some key advancements include:
1. High-Performance Materials
Earlier generations of seals primarily used nitrile rubber or neoprene. Today, the adoption of advanced elastomers like hydrogenated nitrile (HNBR), polytetrafluoroethylene (PTFE), and polyurethane has improved wear resistance, chemical compatibility, and heat tolerance.
These modern materials are particularly valuable in environments where hydraulic fluids vary, temperatures spike, or equipment runs for extended cycles without downtime.
2. Enhanced Seal Geometry
In addition to material selection, precision in the shape and profile of a seal is just as critical. Modern designs, for instance, feature multi-lip configurations, asymmetric sealing lips, and specially contoured surfaces to reduce friction and increase sealing efficiency. As a result, this innovation reduces wear and energy loss, thereby enabling smoother performance and longer service intervals.
3. Self-Lubricating Capabilities
Some seals now incorporate materials or coatings that provide self-lubrication, further reducing friction and heat generation during high-speed operations. This feature is particularly beneficial in hydraulic motors and rotary applications, where minimizing wear is essential for longevity.
4. Integrated Dust and Wiper Seals
Modern seal systems often include integrated dust or wiper seals that remove dirt and debris from moving surfaces before they contact the main oil seal. This two-tiered defense significantly enhances seal life in harsh operating environments like mining or agriculture.
To learn more about high-performance hydraulic oil seal capabilities and their industrial applications, exploring specialized service providers with expertise in material science and seal customization can be valuable.
Impact on Equipment Longevity
Hydraulic oil seal innovations do more than reduce fluid leaks—they directly affect the long-term durability of entire systems. Here’s how:
• Reduced Internal Leakage
To begin with, modern seals maintain tighter tolerances and greater resilience under pressure, helping reduce internal leakage within hydraulic actuators. Consequently, this improves force efficiency and reduces the energy needed to compensate for pressure loss.
• Less Frequent Maintenance
The enhanced durability of today’s seals means longer service intervals and fewer unplanned shutdowns. For industries with round-the-clock operations, this translates to lower maintenance costs and greater productivity.
• Improved Protection Against Contaminants
Advanced sealing systems effectively block dust, water, and particles from entering hydraulic chambers. This not only extends the life of the seal itself but also protects internal surfaces like rods and cylinders from abrasion and corrosion.
• Enhanced Temperature and Chemical Resistance
Industrial environments often involve exposure to aggressive fluids or temperature fluctuations. Modern oil seals can maintain integrity under a wide range of conditions, ensuring stability in both cold and high-heat applications.
Integrating Sealing Solutions into Lifting and Material Handling Systems
Hydraulic seals are a backbone component in lifting and vertical mobility systems, which are widely used across industries to streamline operations and improve workplace safety. As businesses look to improve vertical storage, maintenance access, and equipment transport, reliable lifting mechanisms are essential.
One such solution that benefits from advanced hydraulic sealing is the Vertical Mast Lift—a compact and efficient lifting platform designed for indoor or space-restricted environments. The Benefits of Installing a Vertical Mast Lift extend beyond space optimization; they include enhanced operational safety, better load stability, and ease of maintenance—all of which depend on hydraulic systems functioning without leaks or performance dips.
Reliable oil seals in such applications help prevent failures, ensure smoother lift operations, and support the structural longevity of hydraulic components.
Conclusion
The innovations in hydraulic oil seal technology are not merely technical upgrades—they are strategic improvements that directly influence how long and how well industrial systems perform. As industries demand faster, more precise, and more reliable machinery, every component must deliver long-term value.
Through advanced materials, smarter designs, and better integration into broader systems, modern oil seals are helping industries reduce downtime, extend maintenance cycles, and protect their investments. In an era where productivity and sustainability go hand in hand, upgrading to innovative sealing solutions is a small step with a major impact.
From heavy-duty machinery to precision vertical lifts, the evolution of sealing components is quietly shaping the future of hydraulic engineering—sealing not just fluids, but the long-term success of industrial operations.